自1969年集成光路的概念被提出以來(lái),科學(xué)家們就一直為實(shí)現(xiàn)大規(guī)模光子芯片而進(jìn)行不懈努力,種類(lèi)繁多的光子芯片都得到了較為深入的研究,包括石英玻璃光子芯片、聚合物光子芯片、以硅為代表的半導(dǎo)體光子芯片等,這些光子芯片技術(shù)均有各自的優(yōu)勢(shì)與不足。種種技術(shù)方案表明,實(shí)現(xiàn)高質(zhì)量的大規(guī)模集成光子芯片需要優(yōu)越的材料特性和先進(jìn)的加工手段完美結(jié)合。
鈮酸鋰(LN)晶體具有寬透射窗口、高非線(xiàn)性系數(shù)、高折射率和大電光系數(shù)等優(yōu)異特性,是光子集成器件襯底材料的重要候選者,被譽(yù)為“光子學(xué)中的硅”。表1對(duì)比了鈮酸鋰薄膜(LNOI)與幾種典型的光子集成器件襯底材料的性能。
表1 典型光子集成平臺(tái)對(duì)比
我國(guó)鈮酸鋰薄膜技術(shù)的發(fā)展與產(chǎn)業(yè)化方面走在世界前列,已有全球知名的鈮酸鋰薄膜品牌(NanoLN),這為高品質(zhì)鈮酸鋰光子器件的制備奠定了重要材料基礎(chǔ)。將鈮酸鋰晶體材料與合適的加工技術(shù)相結(jié)合,可實(shí)現(xiàn)多功能的高品質(zhì)鈮酸鋰光子結(jié)構(gòu)的制備,進(jìn)而為光子芯片提供高性能的核心器件。
在過(guò)去的不到十年中,國(guó)際上發(fā)展了三條重要的鈮酸鋰光子芯片的制造技術(shù)路線(xiàn),能夠用于獲得高品質(zhì)、具有實(shí)用意義的光子芯片原型器件。這三種技術(shù)路線(xiàn)分別為飛秒激光直寫(xiě)結(jié)合聚焦離子束刻蝕技術(shù)、電子束曝光結(jié)合離子刻蝕技術(shù),以及飛秒激光光刻輔助化學(xué)機(jī)械拋光技術(shù)。
飛秒激光直寫(xiě)結(jié)合聚焦離子束刻蝕
飛秒激光由于具有顯著降低的熱效應(yīng)、可突破衍射極限的加工精度、可對(duì)透明材料內(nèi)部進(jìn)行三維加工等獨(dú)特優(yōu)勢(shì),被廣泛用于微納加工領(lǐng)域。2015年,利用飛秒激光直寫(xiě)結(jié)合聚焦離子束刻蝕來(lái)制備高品質(zhì)鈮酸鋰微腔的技術(shù)路線(xiàn)被第 一次提出,并成功實(shí)現(xiàn)了品質(zhì)因子(Q值)超過(guò)105的微盤(pán)腔的制備,突破了當(dāng)時(shí)國(guó)際新高紀(jì)錄。
該方案使用鈮酸鋰薄膜/二氧化硅/鈮酸鋰襯底的材料作為樣品,主要技術(shù)步驟包括:
1)將鈮酸鋰薄膜樣品置入水中,利用飛秒激光在薄膜晶圓上燒蝕出微盤(pán)輪廓;
2)使用聚焦離子束(FIB)對(duì)微盤(pán)側(cè)壁進(jìn)行研磨拋光,以降低側(cè)壁散射損耗;
3)將樣品放入質(zhì)量分?jǐn)?shù)為5%的氫氟酸(HF)溶液中進(jìn)行化學(xué)腐蝕,選擇性地去除鈮酸鋰薄膜下方的二氧化硅層,在鈮酸鋰圓盤(pán)下形成二氧化硅支柱;
4)通過(guò)高溫退火,減少了鈮酸鋰微盤(pán)的晶格損傷,降低了圓盤(pán)內(nèi)部的散射損耗,提高了微盤(pán)Q值,如圖1所示。經(jīng)過(guò)工藝優(yōu)化,該技術(shù)路線(xiàn)可將Q值進(jìn)一步提高至9.6×106。
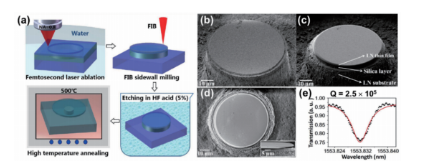
圖1 利用飛秒激光直寫(xiě)結(jié)合聚焦離子束刻蝕技術(shù)制備的高品質(zhì)因子鈮酸鋰微腔。(a)鈮酸鋰微腔制備流程圖;(b)飛秒激光燒蝕后形成的微柱體SEM圖像;(c)聚焦離子束刻蝕后形成的微柱體SEM圖像;(d)經(jīng)過(guò)化學(xué)腐蝕和高溫退火后,直徑為55 μm微盤(pán)的SEM俯視圖,插圖為微盤(pán)SEM側(cè)視圖;(e)微腔在1553.83 nm諧振波長(zhǎng)附近的透射光譜 (虛線(xiàn))及洛倫茲擬合曲線(xiàn)(實(shí)線(xiàn))
該項(xiàng)鈮酸鋰光子結(jié)構(gòu)加工技術(shù)不僅可以加工單個(gè)光子結(jié)構(gòu),還可以實(shí)現(xiàn)多個(gè)光子結(jié)構(gòu)的集成。圖2展示了利用飛秒激光直寫(xiě)結(jié)合聚焦離子束刻蝕技術(shù)制備的幾個(gè)集成光子結(jié)構(gòu)。
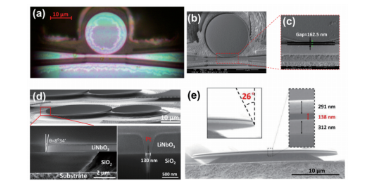
圖2 利用飛秒激光直寫(xiě)結(jié)合聚焦離子束刻蝕技術(shù)制備的集成光子結(jié)構(gòu)。(a)~(c)鈮酸鋰微盤(pán)腔與波導(dǎo)的片上集成;(d)耦合鈮酸鋰微盤(pán)光子學(xué)分子;(e)垂直集成的雙盤(pán)鈮酸鋰微腔
電子束曝光結(jié)合離子刻蝕技術(shù)于2014年由哈佛大學(xué)研究組提出。該技術(shù)路線(xiàn)的主要工藝流程如圖3所示,核心步驟包括電子束光刻掩模、干法刻蝕及基于電子束剝離(lift-off)工藝的金屬電極制備。通常制備基底材料為鈮酸鋰薄膜晶圓,由600 nm厚的鈮酸鋰薄膜、2 μm厚的二氧化硅及500 μm厚的硅襯底三層結(jié)構(gòu)組成。
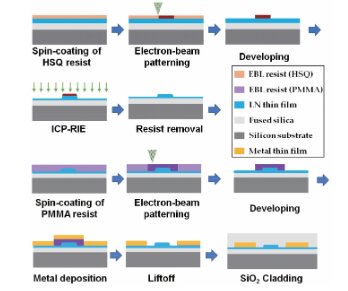
圖3 電子束曝光結(jié)合離子刻蝕的鈮酸鋰光子芯片的制造工藝流程圖
經(jīng)過(guò)優(yōu)化氬離子刻蝕參數(shù)和覆蓋二氧化硅包層,該技術(shù)可將微腔的本征Q值提升至107量級(jí)。
圖4為哈佛大學(xué)研究組利用電子束曝光結(jié)合離子刻蝕技術(shù)制備的低損耗光波導(dǎo),經(jīng)過(guò)覆蓋二氧化硅包層,直波導(dǎo)的損耗可低至約0.027 dB/cm。該技術(shù)利用現(xiàn)有較為成熟的電子束曝光工藝與離子刻蝕技術(shù),一旦找準(zhǔn)工藝條件,就可以快速?gòu)?fù)制其技術(shù)路線(xiàn),進(jìn)行小批量光子原型器件的研發(fā),因此被多個(gè)國(guó)內(nèi)外研究團(tuán)隊(duì)所采納。
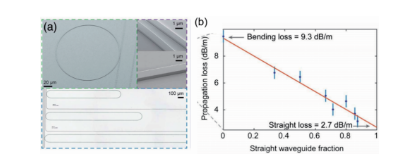
圖4 制備的波導(dǎo)耦合微環(huán)和跑道型微腔以及傳輸損耗測(cè)量。(a)波導(dǎo)耦合微環(huán)腔和跑道型微腔的SEM圖(上方) 以及跑道型微腔的設(shè)計(jì)圖(下方);(b)利用不同臂長(zhǎng)的跑道型微腔獲得的傳輸損耗,激發(fā)波長(zhǎng)為1590 nm
如上所述,飛秒激光直寫(xiě)與聚焦離子束刻蝕相結(jié)合,可以制備出Q值大于106的鈮酸鋰薄膜微盤(pán)腔。然而,人們通常需要更高Q值的回音壁模式(WGM)微諧振腔,以在低泵浦功率下實(shí)現(xiàn)高效的非線(xiàn)性過(guò)程。聚焦離子束刻蝕不可避免地會(huì)留下納米量級(jí)的表面粗糙度,從而將鈮酸鋰薄膜微腔的Q值限制在107以下。
鑒于此,飛秒激光光刻輔助化學(xué)機(jī)械拋光(PLACE)技術(shù)于2018年被提出并報(bào)道,實(shí)現(xiàn)了Q值高達(dá)4.7×107的鈮酸鋰微盤(pán)腔的制備。近年來(lái),通過(guò)進(jìn)一步完善工藝,利用該技術(shù)已經(jīng)能夠?qū)⑩壦徜囄⑶坏钠焚|(zhì)因子提高至108以上,這一品質(zhì)因子的新紀(jì)錄已經(jīng)接近鈮酸鋰材料的本征吸收極限。
PLACE技術(shù)的獨(dú)特優(yōu)勢(shì)在于該技術(shù)采用化學(xué)機(jī)械拋光(CMP)來(lái)選擇性地去除或刻蝕襯底材料以完成芯片構(gòu)圖,其主要步驟如圖5所示。傳統(tǒng)的CMP只是一種提高表面光滑度的手段。
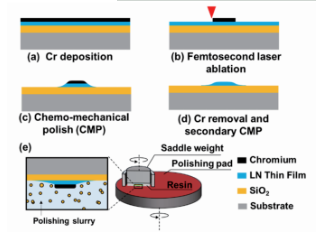
圖5 飛秒激光光刻輔助化學(xué)機(jī)械拋光(PLACE)的鈮酸鋰光子芯片的制造流程圖。(a)在LNOI上沉積鉻(Cr)層;(b)飛秒激光燒蝕Cr薄膜形成掩模圖案;(c)通過(guò)化學(xué)機(jī)械拋光將掩模圖案從Cr膜轉(zhuǎn)移到LNOI上;(d)移除Cr,并進(jìn)行二次化學(xué)機(jī)械拋光;(e)化學(xué)機(jī)械拋光原理與實(shí)驗(yàn)裝置圖
同時(shí),PLACE技術(shù)還可以實(shí)現(xiàn)傳輸損耗低至0.027 dB/cm的脊型鈮酸鋰光波導(dǎo)的制備。制備鈮酸鋰光波導(dǎo)的工藝流程與制備微盤(pán)腔的基本相同,區(qū)別在于飛秒激光直寫(xiě)光刻之后,保留金屬鉻掩模的鈮酸鋰薄膜區(qū)域是狹長(zhǎng)的條形,從而在經(jīng)過(guò)化學(xué)機(jī)械拋光、鉻膜腐蝕等后續(xù)處理后,只留下脊型鈮酸鋰波導(dǎo)結(jié)構(gòu)。圖6為利用PLACE技術(shù)所制備的鈮酸鋰環(huán)形微腔和脊型光波導(dǎo)結(jié)構(gòu)。
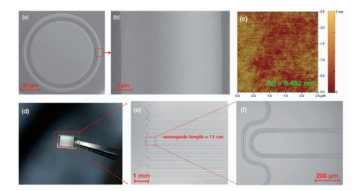
圖6 基于PLACE技術(shù)制備的鈮酸鋰微環(huán)腔和光波導(dǎo)。(a)(b)鈮酸鋰微環(huán)腔的SEM 俯視圖及其局部放大圖;(c)AFM測(cè)得微環(huán)表面的粗糙度為0.452 nm;(d)長(zhǎng)度為11 cm的鈮酸鋰光波導(dǎo)的數(shù)碼照片;(e)(f)鈮酸鋰光波導(dǎo)的光學(xué)顯微圖
研究人員利用以上的技術(shù)途徑,在鈮酸鋰薄膜襯底上實(shí)現(xiàn)了一批高品質(zhì)因子的鈮酸鋰光子原型器件,包括波導(dǎo)耦合分束器、可重構(gòu)多功能芯片、光子延時(shí)線(xiàn)、微腔激光器、波導(dǎo)放大器、高速光調(diào)制器、微波光子芯片等。
同時(shí),基于這些光子結(jié)構(gòu)實(shí)現(xiàn)了多種非線(xiàn)性光學(xué)效應(yīng),包括自然準(zhǔn)相位匹配高效非線(xiàn)性諧波、電光可調(diào)光機(jī)械力學(xué)效應(yīng)、電光可調(diào)寬帶光學(xué)頻率梳、新型多邊形模式物理效應(yīng)、雙腔光子學(xué)分子非線(xiàn)性效應(yīng)、雙層腔高Q值腔外回音壁模式效應(yīng)等。
利用飛秒激光直寫(xiě)結(jié)合聚焦離子束刻蝕技術(shù)、電子束曝光結(jié)合離子刻蝕技術(shù)、飛秒激光光刻輔助化學(xué)機(jī)械拋光技術(shù),實(shí)現(xiàn)了超高品質(zhì)因子微盤(pán)腔、超低損耗光波導(dǎo)等集成光路中的關(guān)鍵核心光子結(jié)構(gòu)的制備。聚焦離子束技術(shù)的制造效率相對(duì)較低,目前不在產(chǎn)業(yè)界的考慮范圍,另外兩條技術(shù)途徑目前都已產(chǎn)生了許多令人矚目的成果,且都進(jìn)入了產(chǎn)業(yè)界的視野。
原理上來(lái)講,化學(xué)機(jī)械拋光技術(shù)能夠?qū)⒐庾咏Y(jié)構(gòu)表面的散射損耗降至極低水平,從而使得所制備的鈮酸鋰光子器件的損耗接近材料本征吸收損耗。該技術(shù)已逐漸從實(shí)驗(yàn)室走向?qū)嶋H應(yīng)用,可以預(yù)見(jiàn),未來(lái)該技術(shù)將會(huì)使光子集成領(lǐng)域的學(xué)術(shù)界和產(chǎn)業(yè)界受益匪淺。
當(dāng)然,該技術(shù)也有一些問(wèn)題有待解決,如受限于有限的鉻與鈮酸鋰之間的刻蝕比率,鈮酸鋰微腔與平面集成波導(dǎo)之間存在較大的間隔,很難做到臨界耦合。盡管微腔的Q值已突破108,但脊型波導(dǎo)的損耗卻沒(méi)有獲得相應(yīng)進(jìn)展;大規(guī)模集成展露曙光,然而要實(shí)現(xiàn)復(fù)雜的功能集成,尚需時(shí)日。片上激光器已被實(shí)現(xiàn),但還不是單模激光,且還沒(méi)實(shí)現(xiàn)激光的片上非線(xiàn)性頻率變換。鈮酸鋰光子集成技術(shù)的未來(lái)充滿(mǎn)了機(jī)遇與挑戰(zhàn),尚有巨大發(fā)展空間等待著人們?nèi)ヌ剿鳌?/span>
本文改寫(xiě)自《光學(xué)學(xué)報(bào)》文章——超低損耗鈮酸鋰光子學(xué),原文請(qǐng)點(diǎn)擊“閱讀原文”查看。